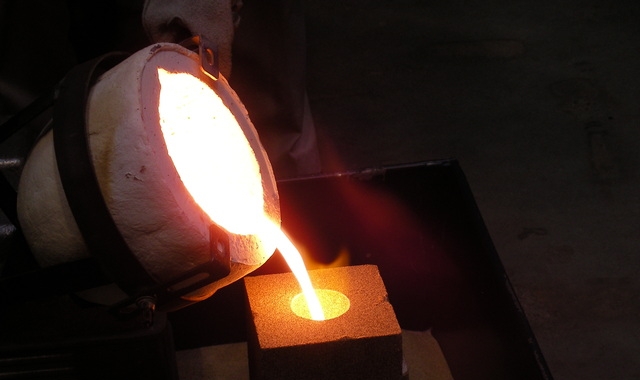
ダイハツ工業は2017年8月24日、エンジンやトランスミッションなどに使用する鋳造部品の生産に用いる砂型を、3Dプリンターで製作するために必要な新技術を開発したと発表した。部品試作の短期化や低コスト化に加え、砂の100%リサイクルによるランニングコストの抑制や環境負荷低減への貢献も期待される。
これまで鋳造部品の製作は、まず木型や金型を使用して砂型を製作し、そこに溶融した鉄やアルミニウムなどの金属を流し込んでいた。しかし、木型や金型の製作には高度な技能が必要であり、また製作期間の長期化が課題となっていた。近年では3Dプリンターの活用により砂型を直接製作する技術が進歩してはいたが、溶融温度の高い鉄系部品では砂型に割れが発生するなど対応が困難だった。
今回、同社は砂型に使用する砂の表面に酸触媒などで2層コーティングする新技術を開発し、人工砂でありながら常温で高速硬化する「フラン自硬性プロセス」で造型することに成功した。3Dプリンターを使用した鉄系部品の砂型製作が可能となったことで、試作作業を短期化できるとしている。既存の3Dプリンターと量販の人工砂が使用できるため汎用性も高く、再コーティングを施せば使用した人工砂を100%リサイクルできるため、ランニングコストの抑制にも貢献する見込みだ。