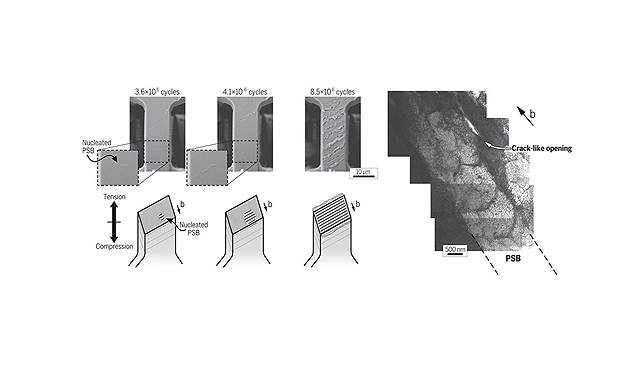
米ジョンズ・ホプキンス大学の研究チームが、金属疲労の初期段階で生じる微視的結晶構造変化を、電子顕微鏡内における「その場(in situ)」ミクロ疲労試験によって捉えることに成功した。通常の引張試験における降伏強度より遥かに小さい応力振幅の繰り返しサイクルによって不可逆的な転位集積が生じ、サイクル数の増加に伴ってミクロ亀裂が発生する過程を実験的に観察したものである。最終的に材料全体の疲労破壊につながる初期メカニズムを明らかにしたものであり、将来的に橋梁や航空機などにおける疲労破壊の予知手法確立に展開できると期待される。研究成果が、2020年10月9日の『Science』誌に公開されている。
金属材料は降伏強度より小さい応力負荷を受けても破断することはなく、弾性応力範囲内であれば、負荷を取り除くと元の形状を回復する。だが、これはあくまでもマクロな観察結果であり、弾性範囲内の小さい応力であっても、原子レベルのミクロな視点では一部の原子がもとあった場所に戻らない不可逆的な振る舞いを起こす。このような応力負荷が周期的に繰返されると、不可逆的な結晶構造の変化、即ち不可逆的な転位運動が蓄積されることによってミクロ亀裂を生じ、やがて亀裂が拡大、伝播して、部材全体や構造全体の巨視的な破壊に至る。これが疲労破壊として知られる現象のメカニズムだ。1985年の日航ジャンボ機墜落事故では、アルミ合金の圧力隔壁における疲労破壊が原因とされ、また2017年の山陽新幹線の鋼製台車における破断寸前の疲労亀裂発覚も、こうしたメカニズムによるものだ。
最終的な巨視的疲労破壊につながるミクロ亀裂は、定期的な非破壊検査などでも確実に検出できない場合も多く、航空機ではミクロ亀裂が発生、伝播することを前提として、寿命を評価する損傷許容設計が採用され、多数の部品を計画的に交換しているのが現状だ。一方、ミクロ亀裂の発生メカニズムに関する理解が進み、周期的に応力負荷される材料の余寿命を高精度で予測できるようになれば、無条件で計画的に交換するための高額な費用や工程を削減できると考えられ、大きなメリットになる。
これまでミクロ亀裂発生の原因を把握する研究の大半は、亀裂発生の前後を詳細に観察することにより、破断面や材料表面に発生するストライエーション(注:亀裂先端に形成される波状構造のこと)が、不可逆的な転位運動と関連することなどを明らかにしてきた。しかし、引張試験と同程度の大きさの試験片を用いるのではμmレベルのスケールの損傷初期過程を追跡できないため、研究チームは、断面12×13μm 、標点距離27μmの単結晶Ni超小型試験片を用い、走査電子顕微鏡内で「その場(in situ)」観察を行いながらミクロ疲労試験を実施することにチャレンジした。
その結果、巨視的に観察されるストライエーションに対応する、転位の固執すべり帯(PSB:Persistent Slip Band、注:応力繰り返しにより発達したすべり帯で、研磨などによって除去できないもののこと。ミクロ亀裂の発生につながると考えられている)の初期構造を明らかにするとともに、約0.5μmのミクロ亀裂を観察することに成功した。この手法を発展させ、ミクロ亀裂発生の初期過程を特定することにより、将来的に疲労寿命予測手法を確立できると、研究チームは期待している。
関連リンク
New method can pinpoint cracks in metal long before they cause catastrophes